蓄热氧化炉(RTO)废气治理技术在实际应用中存在以下主要技术缺点:
1. 高能耗与运营成本高
燃料消耗大:需长期维持700~1000℃高温氧化环境,尤其在废气浓度低时需额外补充天然气或燃油,能耗显著增加。
初期投资高:陶瓷蓄热体、耐高温阀门/风机等核心部件成本高昂,且设备整体体积大,安装费用高。
维护成本高:陶瓷蓄热体易堵塞或热应力破损(需定期更换);燃烧室及管道的高温腐蚀问题需频繁检修,增加运维负担。
2. 对废气成分的适应性差
含卤素废气(如氯、氟):高温下可能生成二噁英、HCl等有害副产物,需额外配置二燃室(1100℃以上)和急冷装置,工艺复杂化。
含硫/氮有机物:氧化过程产生SOx、NOx等二次污染物,需配套脱硫脱硝设施,增加系统复杂性和成本。
高沸点或黏性物质:废气中含焦油、漆雾等易黏附在蓄热体表面,导致堵塞和热效率下降。
3. 运行条件要求苛刻
废气浓度范围受限:浓度过低时需补燃,经济性差;浓度过高时需稀释或旁通,处理效率降低。
需连续稳定运行:间歇性生产或废气流量/浓度波动大的场景易导致蓄热体温度失衡,影响净化效率(如VOCs去除率从99%降至90%以下)。
进气预处理要求高:需严格过滤颗粒物(PM)和水分,否则会加速蓄热体堵塞或腐蚀。
4. 设备体积与场地限制
占地面积大:因多室蓄热体结构和庞大热交换系统,RTO设备通常需露天安装,对厂房空间有限的企业适用性差。
热惯性大:启停时间较长(冷启动需数小时升温),不适合短时或频繁启停的工况。
5. 二次污染风险
不完全氧化产物:废气成分复杂或浓度突变时,可能生成CO、醛类等中间产物,需增设后处理单元。
高温气体排放:净化后废气温度仍较高(约100~150℃),直接排放可能造成局部热污染,需增设余热回收或冷却装置。
总结
RTO技术虽在VOCs高效处理中表现突出,但其能耗、成分适应性、运行稳定性及二次污染控制等缺陷仍需通过工艺优化(如沸石转轮浓缩+RTO组合)、材料升级(抗堵陶瓷)或智能调控(动态响应浓度波动)等手段针对性改进。
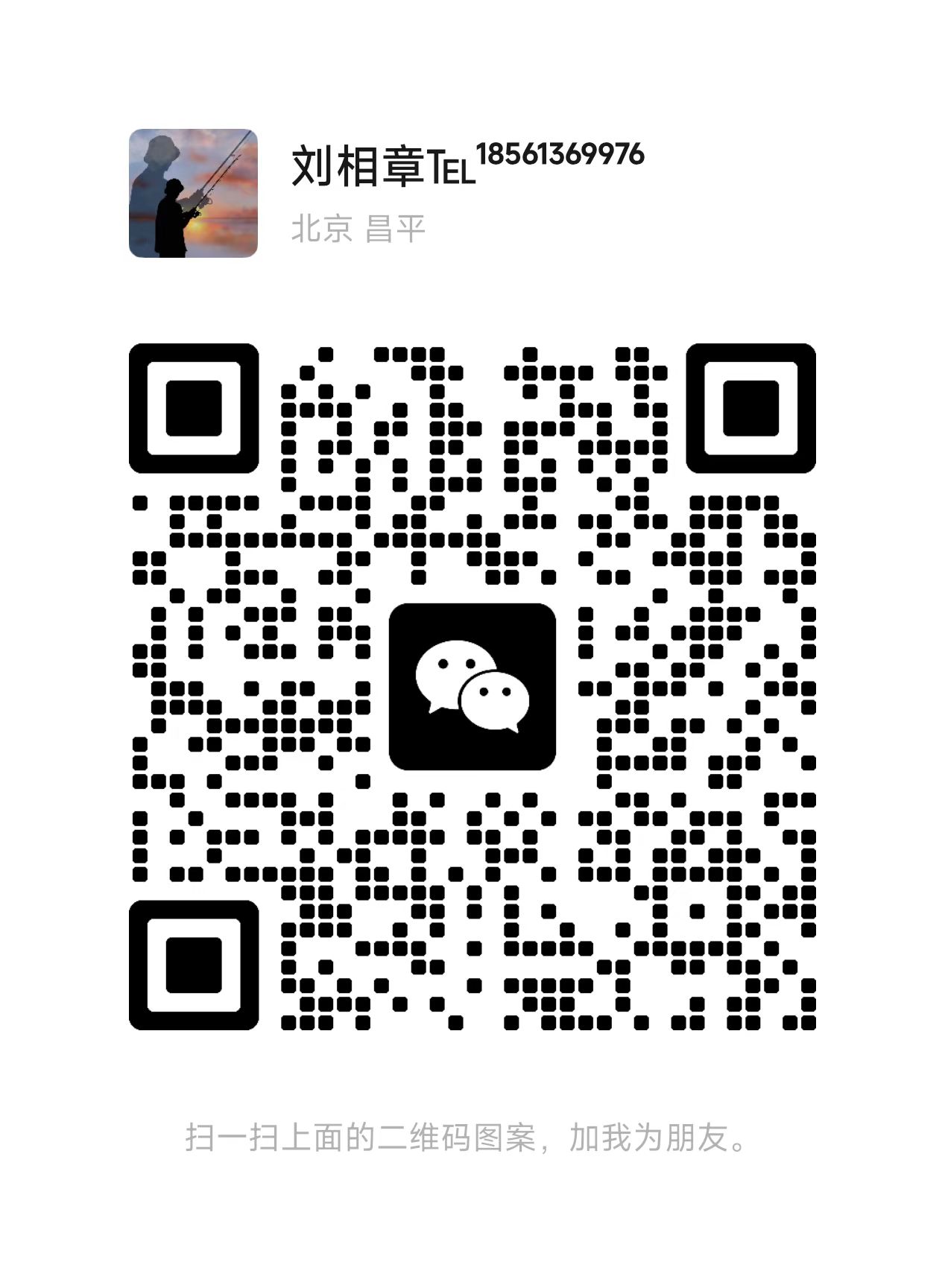