有机废气催化氧化处理技术主要是在催化剂的作用下,将有机废气在较低温度下氧化分解为二氧化碳和水。催化氧化虽然高效,但仍存在以下技术缺点:
催化剂易中毒或失活
敏感成分影响:废气中含硫、卤素、重金属或粉尘等物质会导致催化剂中毒,覆盖活性位点,降低催化效率。
高成本:贵金属催化剂(如铂、钯)价格昂贵,失活后更换频繁,增加运行成本。
严格的预处理要求
需对废气进行除尘、除湿、脱油等预处理,否则颗粒物或油雾会堵塞催化剂孔隙,影响传质效率,增加系统复杂性。
温度控制复杂
能耗问题:低浓度废气需额外加热(通常维持200-400℃),能耗高;高浓度时反应放热可能导致床层超温,需冷却措施。
热管理挑战:温度波动可能损坏催化剂或设备,需精准调控。
浓度适用范围受限
低浓度不经济:废气浓度过低时,维持反应温度需持续加热,经济性差。
高浓度风险:浓度过高可能导致剧烈反应,存在爆炸风险或催化剂烧结。
副产物生成风险
不完全氧化可能产生CO、NOx(高温下)或二噁英(含氯有机物),需二次处理,增加工艺复杂性。
催化剂寿命与维护成本
催化剂寿命有限(通常2-5年),失活后需专业处理(属危废),更换和维护成本高,且可能造成生产中断。
设备投资高
初期需配置催化剂、加热/冷却系统、精密控制系统等,成本高于吸附法或生物法。
操作复杂性
需实时监测温度、浓度、催化剂状态等参数,对操作人员技术要求高,中小企业可能难以稳定运行。
压降与能耗问题
催化剂床层设计不合理可能导致系统压降大,增加风机能耗。
间歇性处理效率低
启动需预热时间,难以应对间歇排放场景,持续运行能耗高。
总结:该技术对废气成分、浓度、操作条件敏感,需综合评估经济性和适用性,尤其在处理复杂废气或中小企业场景中可能面临挑战。
正文完
了解更多服务?立即与我们取得联系!
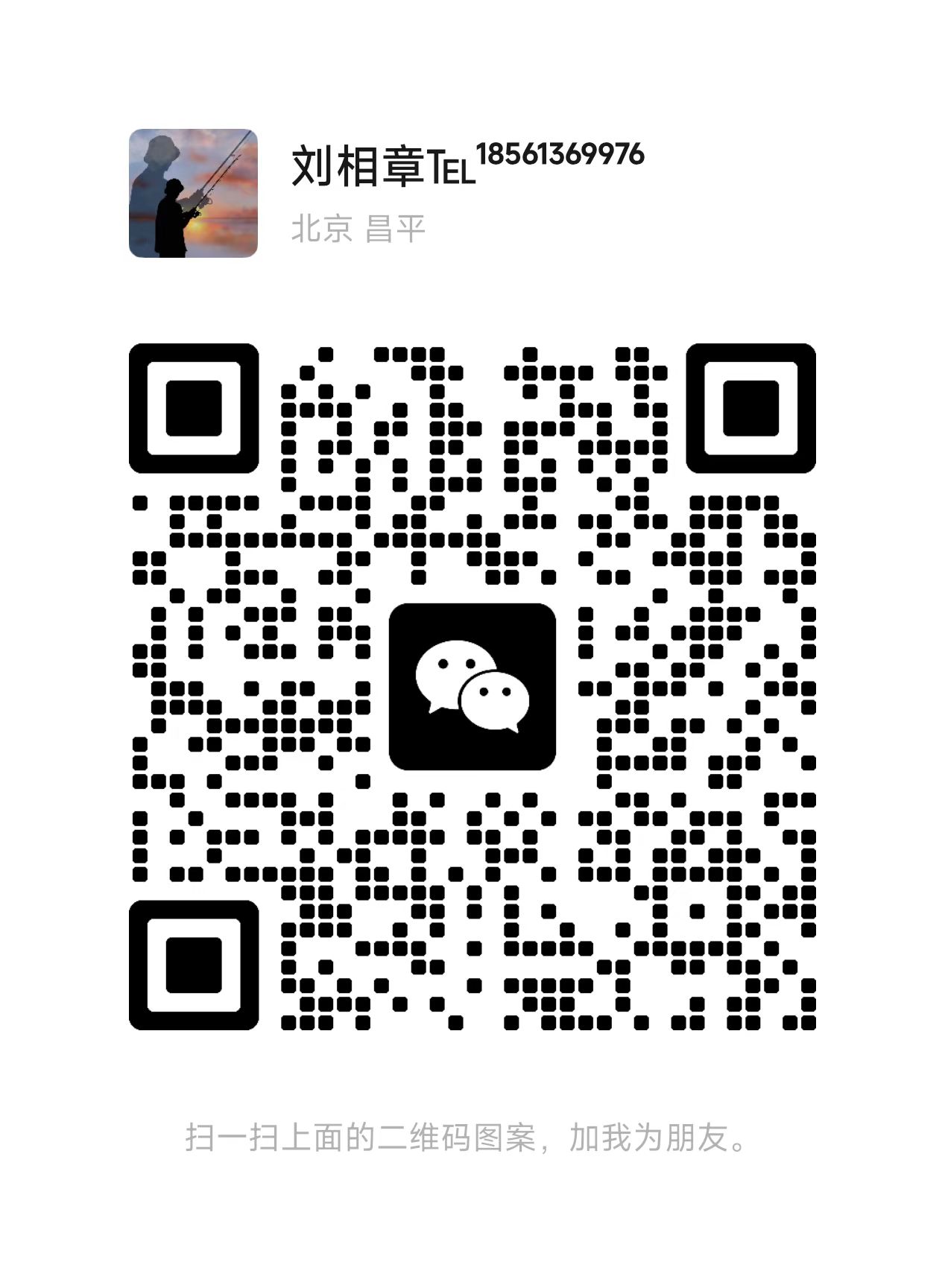