蓄热陶瓷的数量并非越多越好,需根据热效率、压降、设备运行稳定性及经济性综合判断。以下是关键分析:
一、蓄热陶瓷数量增加的潜在优势
热回收效率提升
陶瓷量增加可提高整体蓄热能力,延长热量存储时间,有助于更充分预热废气。例如,陶瓷量翻倍可能将热效率从95%提升至97%,但随着数量增加,效率提升幅度逐渐减小(边际效应)。
缓冲温度波动
陶瓷量多可缓解切换阀门时的温度骤变,增强系统对废气浓度波动的适应性,降低燃烧室温度波动幅度(如从±50℃降至±30℃)。
二、陶瓷数量过多的负面影响
压降显著增加
陶瓷床层增厚或孔密度过高会大幅提高气流阻力。例如,蜂窝陶瓷床层厚度从1.5m增至3m,压降可能从800Pa升至1500Pa,风机能耗增加30%~50%。
高孔密度蜂窝陶瓷(如60×60孔)的狭窄孔道易导致局部堵塞,进一步加剧压降。
成本与空间问题
陶瓷成本占RTO总投资的15%~30%,过量使用会显著提高初期投入。
设备体积受限,床层过厚需扩大蓄热室尺寸,可能超出安装场地限制。
热应力与寿命问题
厚床层易导致气流分布不均,内部与表层温差增大(如温差达200℃以上),引发热应力集中,加速陶瓷开裂(尤其抗热震性差的高铝材质)。
频繁冷热切换时,厚床层的热疲劳效应更明显,陶瓷寿命可能缩短30%~50%。
维护难度上升
陶瓷量多会增加堵塞风险(尤其含颗粒物废气),清灰频率提高,维护成本上升。例如,某案例中陶瓷层过厚导致年维护成本增加40%。
三、合理选型的核心原则
匹配热需求与压降限制
根据废气流量、浓度和切换周期,计算满足热回收效率(通常≥95%)所需的最小陶瓷量,避免冗余设计。
控制压降在合理范围(一般≤1200Pa),避免风机超负荷运行。
优化材质与结构替代增量
选用高孔密度蜂窝陶瓷(如60×60孔)替代低孔密度产品,在相同体积下提升比表面积,减少总用量。
采用分层或板片式结构优化气流分布,降低对陶瓷数量的依赖。
动态适配工况
高浓度废气可减少陶瓷量并缩短切换周期,避免蓄热体过热;
含尘废气需优先抗堵设计(如分层蜂窝),而非单纯增加陶瓷量。
结论
蓄热陶瓷数量需在热效率、压降、成本、寿命间取得平衡:
并非越多越好,过量使用会引发能耗激增、热应力损坏和维护成本上升;
优先通过**材质升级(如高孔密度蜂窝)和结构优化(分层/板片式)**提升性能,而非单纯增加数量;
根据废气特性(温度、腐蚀性、含尘量)动态调整设计,确保系统高效稳定运行。
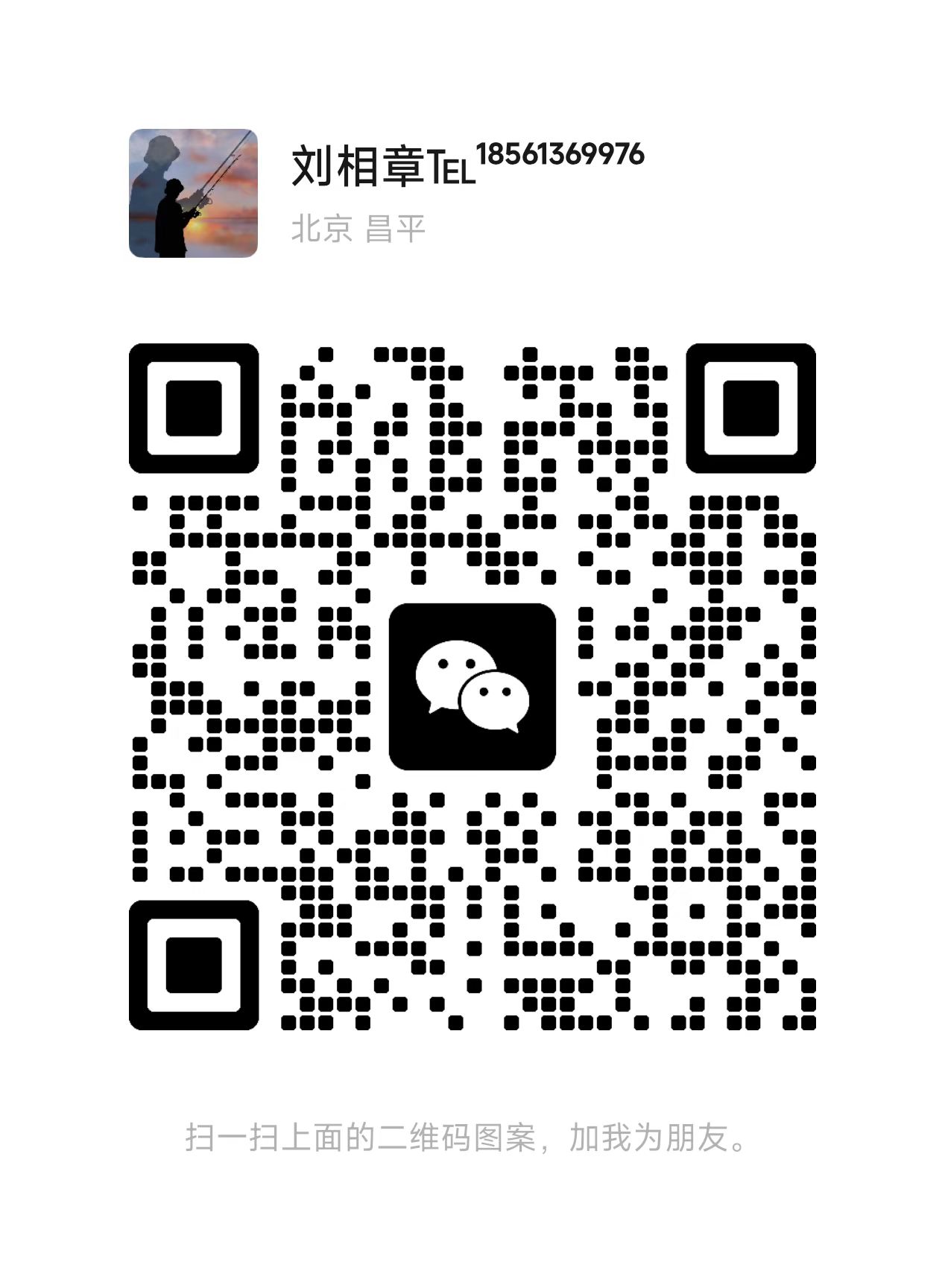