在废气治理系统的管道设计中,降低静电产生的措施需综合考虑材料特性、流体动力学、接地技术及工艺优化,以预防因静电积累引发的火花放电风险(尤其针对易燃易爆废气)。以下是具体的设计与控制措施:
1. 材料选择与表面处理
导电/抗静电材料
优先选用金属管道(如不锈钢、碳钢)并确保良好接地,其导电性可有效导走电荷。若必须使用非金属材料(如玻璃钢、塑料),需添加碳纤维或抗静电剂,使其表面电阻率低于 10^6Ω⋅m(参考GB 12158-2006防静电标准)。
内壁光滑处理
通过抛光或内衬低摩擦系数材料(如聚四氟乙烯涂层),减少气流与管壁摩擦产生的静电,尤其适用于含粉尘或颗粒物的废气。
2. 流速控制与管道设计
流速限制
控制气体流速在安全范围内:
非易燃气体:建议流速 ≤ 25 m/s;
易燃易爆气体:流速需进一步降低(如 ≤ 15 m/s),或通过CFD模拟优化流速分布,避免局部湍流。
管道结构优化
减少弯头、变径等易产生湍流的部件,采用大弧度弯头(曲率半径 ≥ 1.5倍管径)。
避免管径突变,采用渐扩/渐缩设计,平滑过渡以减少电荷分离。
3. 接地与跨接系统
全管道接地网络
金属管道每隔5~10米设置接地极,接地电阻 ≤ 10 Ω(依据NFPA 77标准)。
法兰、阀门等连接处采用导电垫片或跨接铜带(截面积 ≥ 16 mm²),确保电气连续性。
非金属管道接地
内嵌金属网或导电层,并通过多点接地导走电荷。
4. 湿度调节与添加剂
增湿处理
对干燥气体适当增湿(相对湿度 ≥ 60%),通过提高气体导电性促进电荷消散,但需评估对后续工艺(如催化剂、过滤器)的影响。
抗静电剂
在气体中添加微量抗静电剂(如乙二醇、专用离子液),降低介质电阻率,需考虑兼容性及后续处理成本。
5. 静电消除装置
电离式静电消除器
在关键区域(如过滤器入口、弯头下游)安装主动式电离棒,释放异性离子中和电荷。
被动式消电器
使用导电刷或放射性中和器(需符合安全规范),适用于易燃环境。
6. 粉尘与颗粒物控制
预过滤与沉降设计
在管道前端设置旋风分离器或布袋预过滤,减少高摩擦颗粒物(如金属粉尘、树脂颗粒)进入主管道。
导电滤材
过滤器采用导电滤袋(如碳纤维混纺),并直接接地。
7. 监测与防爆措施
静电监测系统
安装静电电位仪或在线电荷监测装置,实时预警电荷积累(阈值通常设定为 ±5 kV)。
防爆设计
在潜在静电积聚点设置泄爆片或惰化系统(如氮气保护)。
管道布局避开爆炸危险区域(按ATEX/IECEx分区要求)。
8. 维护管理
定期清理与检查
清除管道内壁沉积物(尤其绝缘性粉尘),检查接地系统有效性(每季度检测接地电阻)。
操作规范
避免突然启停风机,防止气流剧烈变化导致静电骤增。
应用场景示例
化工VOCs处理系统:采用不锈钢管道+多点接地+电离式消除器,控制流速≤12 m/s;
粉尘废气(如木工车间):内壁抛光碳钢管道+旋风预分离+湿度调节至RH 65%。
通过上述综合措施,可显著降低静电风险,同时兼顾系统效率与安全性。设计时需依据具体废气成分、工况及法规要求(如OSHA 1910.307、GB 50058)进行针对性优化。
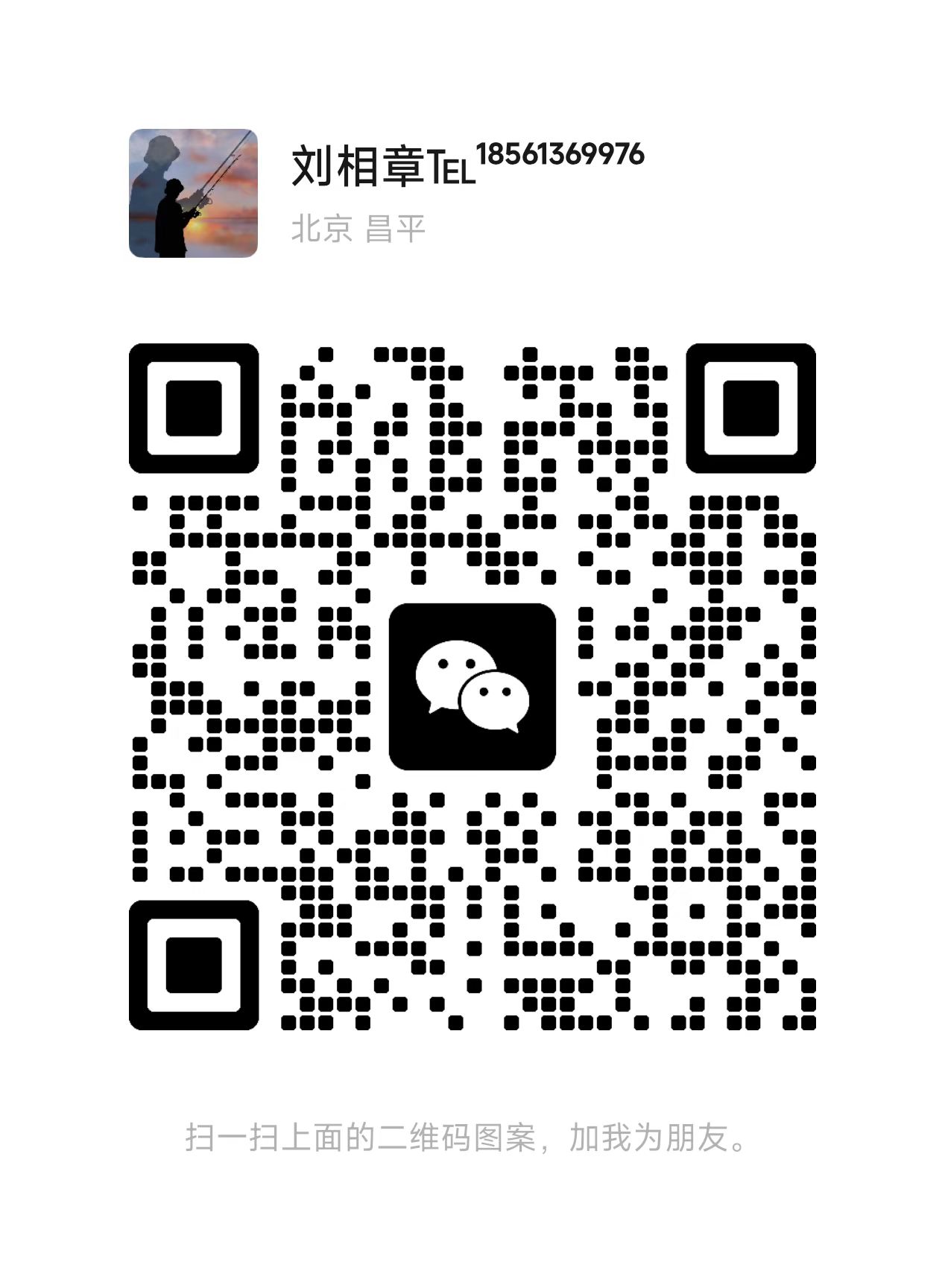