在有机废气治理中,催化氧化温度通常设置在300℃左右,这一选择基于以下多方面的综合考量:
1. 催化剂的活性窗口
催化剂(如贵金属或金属氧化物)在特定温度范围内活性最高:
温度过低(如<200℃):催化剂活性不足,反应速率低,导致有机物(VOCs)无法充分分解,产生中间产物或排放不达标。
温度过高(如>400℃):可能引发催化剂烧结失活,缩短寿命,同时增加副反应(如生成NOx)风险。300℃通常是催化剂活性、稳定性与寿命的平衡点。
2. 有机物分解效率
不同VOCs的起燃温度:苯、甲苯等难降解物质需较高温度(如250-350℃),而催化剂可降低其活化能。300℃能覆盖多数常见VOCs的有效分解需求。
完全氧化需求:确保有机物彻底转化为CO₂和H₂O,避免中间产物(如CO、醛类)的二次污染。
3. 能耗与经济性
能源成本:温度每升高50-100℃,能耗显著增加。300℃在保证处理效率的同时,避免过度依赖外部供热(如天然气或电能),降低运行成本。
余热利用:部分系统通过换热器回收热量,300℃便于余热再利用(如预热进气),提升整体能效。
4. 设备材料与安全性
材料耐受性:高温对设备材质(如不锈钢、陶瓷)要求更高。300℃在常规材料(如304不锈钢)的耐温范围内,减少设备成本。
安全风险:废气中可能含易燃成分,过高温度可能引发燃爆风险,300℃通常远离多数VOCs的自燃点,保障操作安全。
5. 副反应控制
抑制NOx生成:温度超过350℃时,空气中的氮气可能被氧化生成NOx。300℃可有效避免此类副反应,减少二次污染。
减少催化剂中毒:某些含硫、氯的VOCs在高温下易导致催化剂中毒,适中温度可延缓此过程。
6. 实际工程经验
行业标准:大量工程实践表明,300℃在多数场景下能实现90%以上的VOCs去除率,成为行业通用设计参数。
灵活性:针对特殊废气(如高浓度或复杂成分),可通过调节温度(±50℃)优化效果,但300℃作为基准值适用性广。
7.总结
300℃的设置是催化剂活性、处理效率、能耗成本、设备安全及长期稳定性的综合最优解。实际应用中需根据废气成分、浓度、催化剂类型等微调,但这一温度值在大多数场景下实现了技术可行性与经济合理性的平衡。
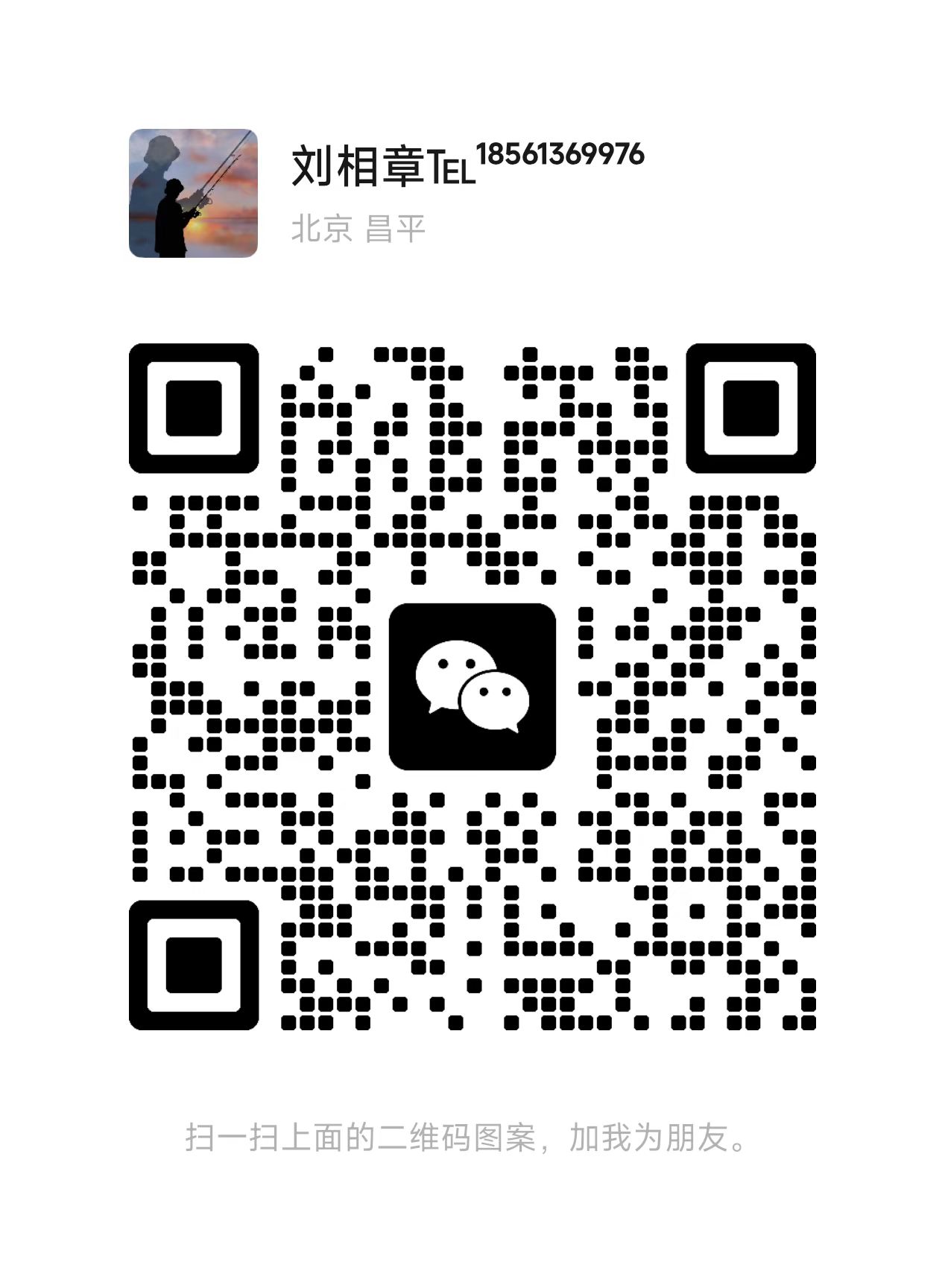